One stop hydraulic hardware product service provider Rotary Joint HYDRAULIC HOSE HOSE FITTING
HOW TO INSTALL HYDRAULIC HOSE FITTINGS?
HYDRAULIC FITTING
4 min read

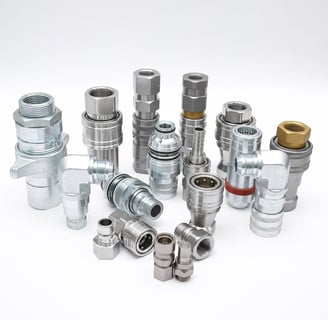
Proper installation of hydraulic hoses and fittings is essential, and most hydraulic hoses and fittings failures are caused by improper installation of the hydraulic hoses and fittings assembly on the hydraulic system.To install hydraulic hoses and fittings correctly, follow these detailed steps to ensure a secure and leak-free connection:
Step-by-Step Installation Process
1. Select the Appropriate hydraulic hoses and fittings
- Choose a hydraulic hoses and fittings that matches the hose size, type, and pressure rating of your hydraulic system. Ensure that the hydraulic hoses and fittings is compatible with the hydraulic fluid and operating conditions.
2. Measure and Cut the hydraulic hoses and fittings
- Use a hydraulic hoses and fittings cutter to measure and cut the hydraulic hoses and fittings to the desired length. Ensure that the cut is clean and straight to prevent fraying or contamination. A precise cut is crucial for a proper fit with the fitting.
3. Prepare the hydraulic hoses and fittings
- Inspect the hydraulic hoses and fittings for any damage or debris. If necessary, clean the hydraulic hoses and fittings threads and ensure they are free from contaminants.
4. Insert the hydraulic hoses and fittings into the Hose
- Align the fitting with the hydraulic hoses and fittings and insert it fully until it reaches the insertion mark (if applicable). This mark indicates how far the fitting should be pushed into the hydraulic hoses and fittings for a proper seal.
5. Crimp or Tighten the hydraulic hoses and fittings
- For Crimped hydraulic hoses and fittings:
- Use a hydraulic crimper, selecting the appropriate die size for your hydraulic hoses and fittings. Place the hose with the attached fitting into the crimper, ensuring it is positioned correctly according to manufacturer guidelines.
- Activate the crimper to secure the hydraulic hoses and fittings onto the hose. Ensure that you achieve a proper crimp without over-tightening, which could damage either component.
- For Field-Attachable hydraulic hoses and fittings:
- If using reusable hydraulic hoses and fittings, apply thread sealant or tape to male threads before tightening. Use a wrench to securely tighten the fitting onto the hydraulic hoses and fittings, ensuring it is snug but not over-tightened.
6. Conduct a Visual Inspection
- After installation, visually inspect all connections to ensure they are properly aligned and free from defects. Check for any signs of misalignment or damage that could lead to leaks.
7. Pressure Test
- Gradually increase hydraulic pressure while monitoring all connections for leaks or abnormal behavior. This step is crucial to verify that all fittings are secure and functioning correctly.
8. Final Inspection
- After testing, conduct a thorough inspection of all fittings and hoses. Look for any signs of leaks or irregularities and address any issues immediately.
Hydraulic hose fittings installation Operation demonstration
1. Twist. The life of the twisted hydraulic hoses and fittings will be significantly shortened, and it is easy to break the hydraulic hoses and fittings or make the connection loose under pressure. The relevant tests show that the hose can reduce its service life by 80% by twisting only 7°.
2. Reserve a spare amount when installing straight pipes. So that it will not be strained or even broken when moving under pressure. Under pressure changes, the hose will have a certain expansion, so be sure to reserve a margin of about 3% to 5%.
3. Pipe clamp in straight section. When the hydraulic hoses and fittings are pressurized, the pressure inside and outside the bending place is unbalanced, and the pipe length will change, so the pipe clamp cannot be set in the bending place to enable it to move freely.
4. Meet the bending radius requirements. Too small a bending radius will tear the reinforced wire braid on the outside of the flexible hose bend, significantly shortening the life of the product.
5. Exercise adaptability. Sufficient length should be reserved to ensure that it has a certain adaptability to motion and avoid friction with other objects.
6. Heat insulation or increase sheath, pipe clamp, avoid friction. Sufficient length should be reserved and friction with other objects should be avoided.
Additional Tips
- Always wear protective gear when working with hydraulic systems.
- Follow manufacturer specifications for torque settings and crimping procedures.
- Regularly maintain your hydraulic system to ensure long-lasting performance.
By adhering to these steps, you can ensure that hydraulic hose fittings are installed correctly, contributing to optimal performance and safety in your hydraulic systems.
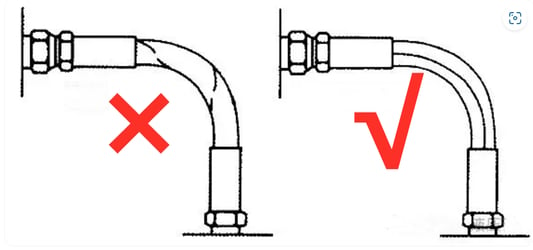
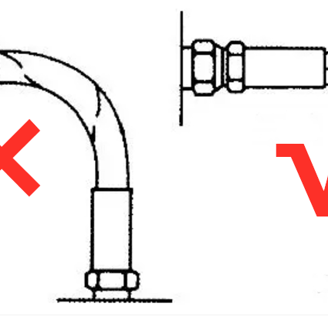
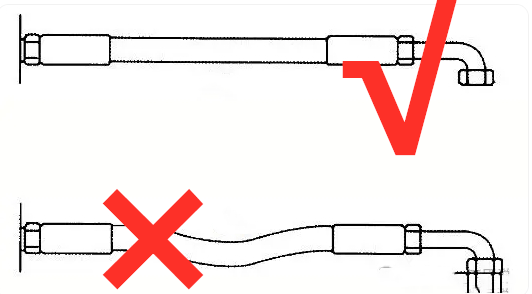
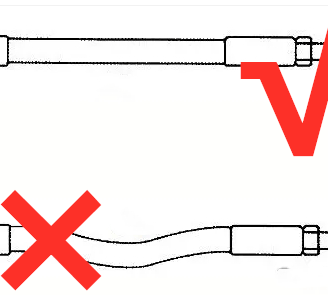
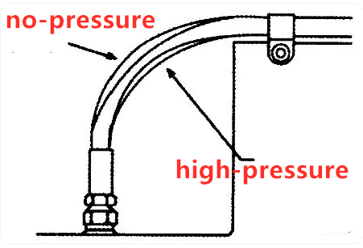
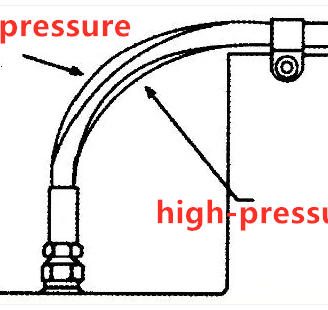
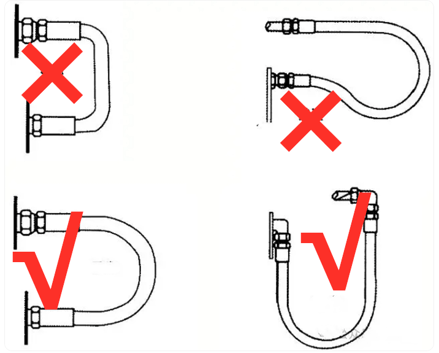
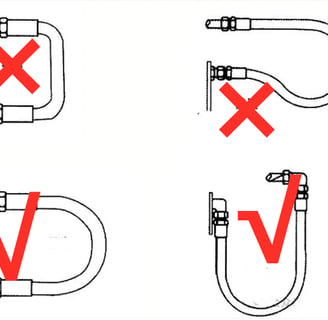
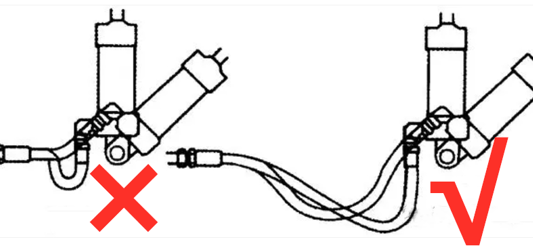
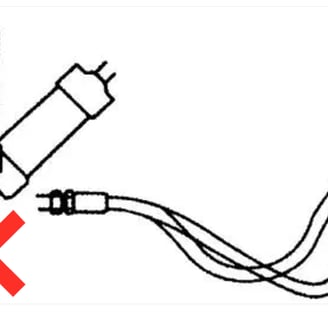
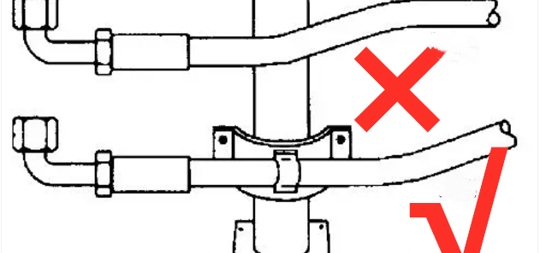
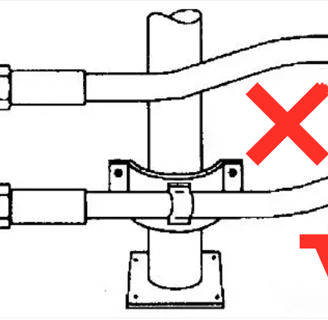
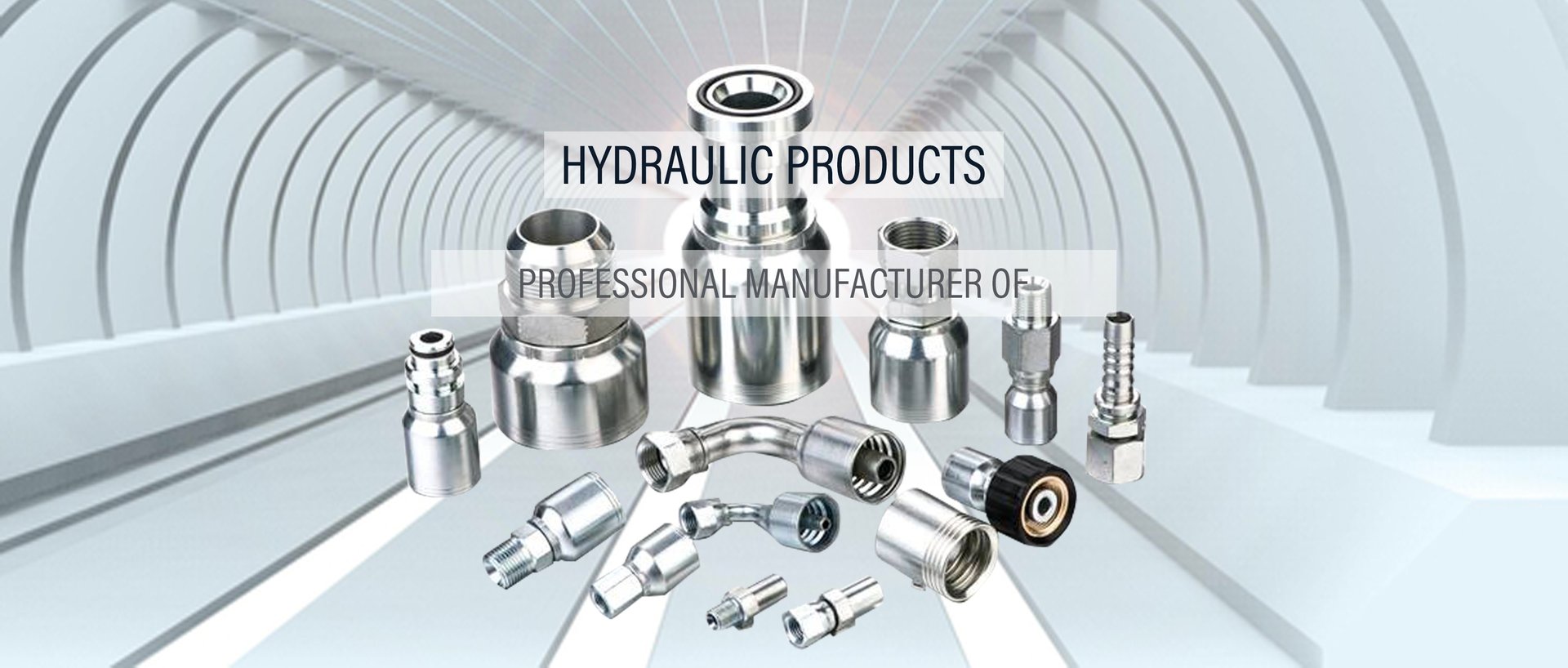