One stop hydraulic hardware product service provider Rotary Joint HYDRAULIC HOSE HOSE FITTING
WHAT IS THE IMPORTANCE OF PROPER HYDRAULIC HOSE ROUTING?
HYDRAULIC HOSE
4 min read
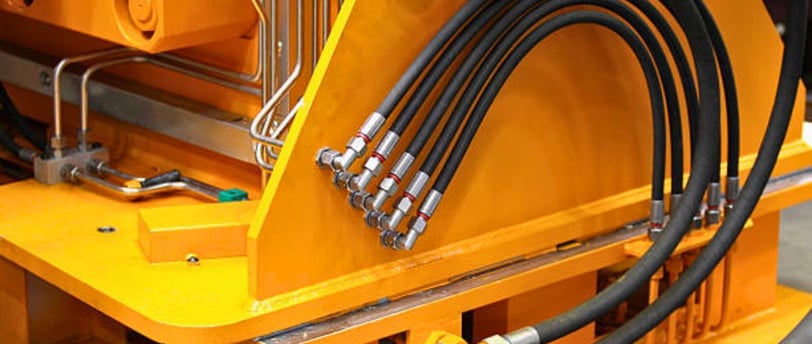
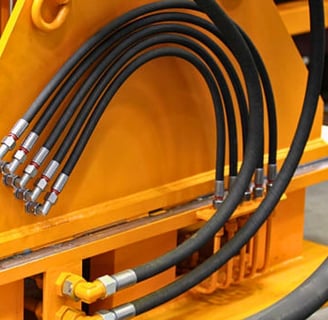
A hydraulic system hose is a flexible pipe that usually consists of three parts: an inner tube, a reinforcement layer, and an outer tube. The inner tube consists of a pressure-resistant material and is used to carry the fluid. The reinforcement layer is a steel wire or fiber used to enhance the pressure resistance of the hose. The outer tube is composed of high-temperature and wear-resistant materials to protect the hose from the external environment.
What is the role of the hydraulic system hose?
The role of the hydraulic system hose is very important, mainly in the following aspects:
1. Distribute and transfer pressure according to the design function.
Hydraulic system hose plays an important role in connecting various hydraulic components in the hydraulic transmission system, carrying pressure signals in a variety of complex environments such as high pressure, high temperature and high frequency vibration, and distributing the flow of oil through the pipeline.
2. Buffer vibration and shock in the hydraulic system.
In the process of pressure conduction in the hydraulic system, due to its characteristics will produce vibration and shock, the hose plays the role of shock absorption and buffering, which can reduce the reflection and fluctuation of pressure waves, so as to avoid damage to the hydraulic system.
3. Harsh working conditions with high oil temperature and high working intensity.
Because the working environment of the hydraulic system is very harsh, the hose needs to withstand high temperature, high pressure and high frequency environment, so it needs to have high temperature, high pressure and wear resistance characteristics to ensure the stability and reliability of the system.
The importance of the hose in the hydraulic system
Many key components in the hydraulic system, such as oil pumps, hydraulic valves and hydraulic cylinders, require hose support and connection. If there is a problem with the hose, it will threaten the normal operation of the entire system. If the pressure on the hose exceeds its carrying capacity, the hose will rupture, resulting in oil leakage and even serious accidents. Therefore, the quality and reliability of the hydraulic system hose is very important.
Replacing a hydraulic hose is a critical maintenance task that requires careful attention to detail to ensure the new hose is installed correctly and safely. Here’s a step-by-step guide to help you through the process:
Tools and Materials Needed
- New hydraulic hose and fittings
- Wrenches and sockets
- Pliers
- Hose cutter
- Deburring tool
- Clean rags
- Grease or assembly lube
- Safety glasses
- Gloves
- Pressure testing equipment (optional)
Step-by-Step Guide
1. Prepare the Work Area
- Safety First: Wear safety glasses and gloves to protect yourself from hydraulic fluid and sharp edges.
- Isolate the System: Turn off the hydraulic system and relieve all pressure. Close any valves to the section of the system you are working on to prevent accidental fluid release.
2. Remove the Old Hose
- Locate the Hose: Identify the hose you need to replace.
- Mark the Position: Mark the position of the old hose and any connections to ensure you can route the new hose correctly.
- Loosen the Fittings: Use wrenches or sockets to loosen the fittings at both ends of the hose. Be careful not to apply too much force, as this can damage the threads.
- Disconnect the Hose: Once the fittings are loose, disconnect the hose from both the supply and return lines. Place a container underneath to catch any residual fluid.
3. Prepare the New Hose
- Measure the Length: Measure the length of the old hose to ensure the new hose is the correct length. If you need to cut the new hose, use a hose cutter to make a clean, square cut.
- Deburr the Ends: Use a deburring tool to smooth out any rough edges on the cut ends of the new hose. This prevents damage to the seals and ensures a proper fit.
- Install the Fittings: Attach the appropriate fittings to the new hose. Apply a small amount of grease or assembly lube to the threads to ensure a smooth installation and prevent galling.
4. Install the New Hose
- Route the Hose: Route the new hose along the same path as the old hose, ensuring it is not twisted or kinked. Use hose clamps or guides to secure the hose and prevent movement.
- Connect the Fittings: Connect the new hose to the supply and return lines. Tighten the fittings securely but do not over-tighten, as this can damage the threads or seals.
- Check for Leaks: Open any closed valves and turn on the hydraulic system. Check the new hose and connections for leaks. If you find any leaks, tighten the fittings as needed or replace any faulty components.
5. Test the System
- Pressure Test: If possible, use a pressure testing device to check the new hose and connections for any leaks or weaknesses. This step is optional but highly recommended for critical applications.
- Run the System: Operate the hydraulic system to ensure everything is functioning correctly. Monitor the new hose for any signs of stress or unusual behavior.
6. Final Inspection and Cleanup
- Inspect the Installation: Double-check all connections and the routing of the new hose to ensure everything is secure and properly installed.
- Clean Up: Dispose of the old hose and any used materials properly. Clean the work area to ensure it is safe and tidy.
Tips for Successful Replacement
- Use the Right Tools: Ensure you have the correct tools for the job to avoid damaging the hose or fittings.
- Follow Manufacturer Guidelines: Refer to the manufacturer’s specifications for the correct type of hose, fittings, and installation procedures.
- Regular Maintenance: Regularly inspect and maintain your hydraulic system to catch issues early and prevent failures.
By following these steps, you can safely and effectively replace a hydraulic hose, ensuring the continued reliability and performance of your hydraulic system.